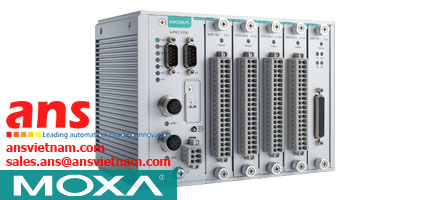
Programmable Controller Series ioPAC 8500 IEC 61131-3 Series Moxa vietnam
Xuất sứ: Moxa VietNam
Nhà cung cấp: Moxa VietNam ANS VietNam
Hãng sản xuất: Moxa
Programmable Controller Series ioPAC 8500 IEC 61131-3 Series Moxa vietnam
Features and Benefits
- Dedicated ARM (RISC) CPUs for the main system and each I/O module
- Millisecond timestamp granularity for digital input and analog input
- Supports 5 kHz sampling rate for analog input
- Pre-recording for analog input data logging
- Supports C/C++ or IEC 61131-3 programming languages
- Compliant with EN 50121-3-2, EN 50121-4, and EN 50155 specifications
- Robust and compact design for harsh environments
- Modular I/O for versatility, flexibility, and scalability
![]() | Precise Data AcquisitionMoxa's ioPAC 8500 RTUs offer up to 40 kHz-level analog input sampling rate, giving engineers the analog data precision they need to correctly analyze events. In addition, the analog input pre-recording function allows the ioPAC 8500 RTUs to continuously record analog input data before an event trigger point for improved data completeness. |
| Sustainable System ReliabilityThe ioPAC 8500 RTU controllers are compliant with EN 50155, EN50121-3-2 and EN 50121-4 railway standards, which require products to withstand high levels of vibration, and provide surge and ESD protection for the power and communication ports. They also support a wide operating temperature range of -40 to 75°C. |
![]() | Easy Data AcquisitionMoxa's ioPAC 8500 RTU controllers come with Moxa's patented Active OPC server and DA-Center software. Active OPC server adds a non-polling architecture to the standard OPC protocol, giving users the advantage of push-based communication from Moxa's controllers to the SCADA systems. DA-Center, on the other hand, provides a standard OPC interface that interacts with Moxa Active OPC Server for real-time data collection. |
![]() | Easy to DeployMoxa's ioPAC 8500 modular RTU controllers support a versatile collection of I/O modules. The compact size and modular design make this ioPAC 8500 ideal for cabinets with limited space, and all of the I/O modules are hot-swappable to allow users to replace the modules without shutting down the system. |
Fast Track Integration for Wayside Condition Monitoring and Preventive Maintenace
This white paper will discuss how railway operators are adopting increasingly sophisticated condition-based maintenance regimes to control costs and improve track performance, some of the key difficulties system integrators need to overcome when deploying wayside condition monitoring systems for railway preventive maintenance, and how using a single condition monitoring platform can save time and costs for deployment and maintenance.
Railway Preventive Maintenance Solutions Flyer
See how Moxa's ioPAC 8500 RTU controllers make railway preventive maintenance easy. The RTUs provide extremely accurate data, giving engineers the information they need to identify anomalous conditions, before failures occur. The ioPAC 8500 RTUs are also designed to work reliably in harsh environments, and modules can be easily replaced to shorten system downtime.
Dimensions
• Computer | |
Main CPU | 32-bit ARM9 192 MHz CPU |
I/O CPU | 32-bit ARM Cortex M4 80 MHz CPU |
OS | Linux |
Clock | Real-time clock with battery backup |
Memory | • SDRAM: 64 MB • Flash: 32 MB • SRAM: 256 KB (battery backup lasts for 1 week) • microSD™ Slot: Up to 32 GB (SD 2.0 compatible) Note: For units operating in extreme temperatures, industrial-grade, widetemperature microSD cards are required. |
• Ethernet Interface | |
LAN | 2 x 10/100 Mbps, 2 MACs (IPs), RJ45 or M12 |
Protection | 1.5 kV magnetic isolation |
• Serial Interface | |
Interface | • 2 RS-232/422/485 ports, software selectable (DB9 male) • 1 RS-232 debug port (4-pin connector) |
Serial Line Protection | 8 kV ESD for all signals |
• Serial Communication Parameters | |
Parity | None, Even, Odd |
Data Bits | 7, 8 |
Stop Bits | 1, 2 |
Flow Control | RTS/CTS, XON/XOFF |
Baudrate | 300 bps to 921.6 kbps |
• Serial Signals | |
RS-232 | TxD, RxD, DTR, DSR, RTS, CTS, DCD, GND, RI |
RS-422 | Tx+, Tx-, Rx+, Rx-, GND |
RS-485-4w | Tx+, Tx-, Rx+, Rx-, GND |
RS-485-2w | Data+, Data-, GND |
• Software Characteristics | |
Automation Languages | C/C++ or IEC 61131-3 |
Protocols | Modbus TCP/RTU (master/slave), SNMP, TCP/IP, UDP, DHCP, BOOTP, SNTP, SMTP |
• Power Requirements | |
Input Voltage | 24 VDC (9 to 48 VDC) |
Input Current | 152 mA @ 24 VDC |
• Physical Characteristics | |
Housing | Aluminum |
Dimensions | • 2-slot version: 114.7 x 135 x 100 mm (4.52 x 5.31 x 3.94 in) • 5-slot version: 190.9 x 135 x 100 mm (7.52 x 5.31 x 3.94 in) • 9-slot version: 292.5 x 135 x 100 mm (11.52 x 5.31 x 3.94 in) |
Weight | • 2-slot version: 1300 g (2.87 lb) • 5-slot version: 2000 g (4.41 lb) • 9-slot version: 2575 g (5.68 lb) |
Mounting | DIN rail (standard), wall (optional) |
Connector | Spring-type terminal block |
• Environmental Limits | |
Operating Temperature | -40 to 75°C (-40 to 176°F) |
Storage Temperature | -40 to 85°C (-40 to 185°F) |
Ambient Relative Humidity | 5 to 95% (non-condensing) |
Shock | IEC 60068-2-27 |
Vibration | IEC 60068-2-6 |
Altitude | Up to 2000 m Note: Please contact Moxa if you require products guaranteed to function properly at higher altitudes. |
• Standards and Certifications | |
Safety | UL 508 |
EMC | EN 55032, EN 55024 |
EMI | FCC Part 15 Subpart B Class A, CISPR 32 |
EMS | IEC 61000-4-2 ESD: Contact: 6 kV; Air: 8 kV IEC 61000-4-3 RS: 80 MHz to 1000 MHz: 3 V/m 1400 MHz to 2100 MHz: 3 V/m 2100 MHz to 2700 MHz: 1 V/m IEC 61000-4-4 EFT: Power: 1 kV; Signal: 0.5 kV IEC 61000-4-5 Surge: Power: 2 kV (L-PE), 1 kV (L-L); |
Rail Traffic | EN 50155*, EN 50121-3-2, EN 50121-4 *Complies with a portion of EN 50155 specifications. Note: Please check Moxa’s website for the most up-to-date certification status. |
• MTBF (mean time between failures) | |
Time | 859,979 hrs |
Standard | Telcordia SR332 |
• Warranty | |
Warranty Period | 5 years |
Details | www.anhnghison.com |